Find answers to the automotive industry’s most-frequently asked IMDS questions here! Our IMDS experts at Tetra Tech share their decades of automotive product compliance experience to help you remain compliant and report with confidence.
IMDS Frequently Asked Questions
1. What is IMDS, and why do I need to use it?
The International Material Data System (IMDS) was developed by DXC Technology to answer the reporting needs of automotive OEMs and their suppliers. With every automotive product comes thousands of parts and pieces with complex substance-level information. The automotive industry needed a way to streamline materials data and ensure they gather high-quality data from every supplier to meet regulations and market requirements.
2. Is IMDS free to use?
The top OEMs continue to invest in IMDS so the reporting software remains free at the baseline for manufacturers and suppliers. For companies with large data needs, however, there might be a need to invest in additional software functionality. Learn more about IMDS here.
3. What am I obligated to report in IMDS?
Automotive part suppliers and manufacturers must report all chemical materials included in a final product as they are delivered to the customer. Substances used in the processing of the parts that are consumed or cured out do not need to be reported — nor does packaging need to be reported. Other requirements differ between OEMs, so pay close attention to their specific instructions.
4. How do I get started in IMDS?
IMDS can be accessed at https://www.mdsystem.com. You’ll want to make sure your browser is up to date and you are using one of the browsers listed in the user manual. It’s also important to note that, although IMDS is an online application, you’ll need to use the buttons within IMDS to navigate through screens rather than using your browser’s buttons. Next, you need to register your company and log in.
5. What is a Material versus a Semi-component, versus a Component?
There are different hierarchies of reporting within IMDS. A Material entry, which can be created by a user or selected from the published materials list, helps you build your MDS. All materials must be homogeneous, meaning they cannot be made up of or separated into different materials. A Semi-component is used to represent a product with layers or a product sold on a roll or as a sheet that is to be cut to size later. It doesn’t have a defined part weight, but rather a specific weight representing its weight per unit volume. A Component captures a product used in a part in an assembly that has a defined weight.
6. What is REC 001?
To provide consistent reporting in the automotive industry, the IMDS Steering Committee requires suppliers to follow several general rules and guidelines set forth notably in IMDS Recommendation 001 (REC 001). These rules are available in the help section of the IMDS website, and they require a thorough understanding to guarantee your submitted parts and assemblies are not rejected. This knowledge will not only speed up your data entry and increase reporting efficiency, it will also increase customer service and reporting success. Please also be sure to refer to IMDS Recommendation 001a and the other case-specific recommendations.
7. What is IMDS 13.0, and how will it affect my reporting?
The newest update — IMDS 13.0 — was released in May 2021 and includes a variety of new features to improve reporting and help you meet new requirements such as the Substances of Concern in Products (SCIP) database. From new reporting fields to new interface features, these tools will give you a more seamless reporting process. Learn more about the specific features here.
8. How can IMDS help me with SCIP reporting?
Since January 2021, the Substances of Concern in Products (SCIP) Database has been required to retain access to EU markets. With data in IMDS there are strategies for using corresponding data fields from IMDS to input information into the SCIP database. Our IMDS experts have created a guide for transferring data between the two databases, which you can access here.
9. What’s a full materials declaration, and why should I use IMDS to create one?
A full materials declaration (FMD) allows you to build a long-term strategy for managing your regulatory compliance. Companies building a FMD need to work with suppliers to gain a composition-level breakdown of components that make up the whole product. IMDS allows users to streamline the collection and storage of these massive amounts of data—as well as an interface where different substances can be updated as needed. Beyond that, IMDS helps compliance professionals put that data to use in customer compliance submissions.
10. Do I need IMDS training?
IMDS can be a complicated system to navigate. Tetra Tech IMDS online training can help your compliance team quickly learn how to use the reporting software efficiently, saving time and cost in reporting. We offer three levels of online IMDS Training: Basic, Standard, and Advanced. These trainings are led by an IMDS instructor with decades of experience and include hands-on activities and quizzes to facilitate learning. Trying to teach yourself IMDS leaves room for errors, confusion and doubts. With a professional IMDS training, you will be able to report accurately and with confidence.
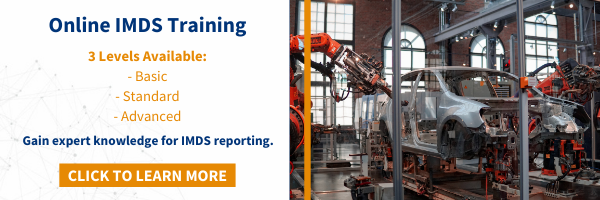
Get IMDS Support
IMDS is a powerful tool that can help you remain compliant. If you are just getting started, Tetra Tech can help you understand how to use IMDS to build full materials declarations, saving you time in the future as new regulations and requirements are added to your compliance demands.
We offer basic, standard and advanced level online training courses for those wanting to build a solid foundation with IMDS. Contact us today to get answers to your additional IMDS questions or to learn how we can support you at [email protected].